The same wheat flour mill line, the same raw grain, and different operating skills will produce significantly different flour milling effects. As far as the grinding effect and equipment operation in wheat flour mill plant are concerned, good technology and equipment are the prerequisite, and the correct operation skills are the guarantee. Only in production practice, in strict accordance with the requirements of process design, comprehensive consideration and careful operation, can the overall effect of the process be brought into play.
Hongdefa 60t/24h wheat flour mill plant
1. The grinding effect of the wheat roller mill
The main equipment in the grinding process is the roller mill machine. In the process design, the grinding effect of the roller mill machine is measured by the stripping rate and the powder extraction rate. Its size is measured by an experimental sieve, but in the process of milling The size of the material is tested by observing the crushing condition of the material after grinding, and the degree of grinding is judged by analysis. In order to find out the problems in process, equipment and operation in time.
2 Operation skills of the roller mill
Determine the best grinding flow rate
Each powder path has a certain flow range. When the flow is too large, the uniformity of material crushing will decrease. If the flow is too small, it is easy to make the feeding state abnormal and the equipment work unstable. In the process of wheat flour mill plant, the best feed rate should be determined according to the condition of the raw grain. At the same time, it is necessary to combine the ambient temperature and humidity to detect the maximum inlet flow rate that can be reached at the time, and gradually adjust the flow to ensure that the materials are distributed to each system in the proportion required by the process design, so as to determine the best inlet flow rate. .
After the optimal feed rate is determined, if the moisture, softness and hardness of the raw grain do not change much, it is not advisable to frequently adjust the feed rate to avoid disrupting the process balance and causing blockage and material drop. If the water content is uneven, the inlet flow rate should be adjusted appropriately. Generally, when the moisture deviates by 1% from the best water entering the roller mill, the flow of entering the roller mill should be reversely adjusted by about 10%. In addition, changes in seasons and climate also have a significant impact on the optimal grinding flow rate. When high temperature, high humidity, and low air pressure, the material is wet and sticky, the grinding flow rate should be appropriately reduced.
3.Final summary
The grinding effect of the roller mill is affected by many factors such as the nature of the incoming material, the flow rate, the feeding effect, the operating parameters of the mill, the surface parameters and processing quality of the grinding roller, the assembly quality and cleaning effect of the grinding roller, and the operation index. To stabilize the grinding effect, ensure that the quality, flow, and particle size of the incoming materials are uniform. The working parameters of the mill are reasonable and accurate, and the operation is safe and reliable. The surface parameters of the roller mill should be adjusted appropriately according to the material properties, flow, grinding requirements, ambient temperature, humidity, etc. To improve equipment operating skills, we must strictly follow the regulations and indicators to perform fine operations. The skin mill system must achieve the target stripping. While strictly controlling the stripping rate and powder extraction rate of each pass, it also controls the total stripping rate, powder extraction rate and the integrity of the bran. The heart mill system must achieve the target powder extraction, while ensuring that the bran flakes contained are not excessively broken, it also extracts the wheat flour of the corresponding quality and particle size in a targeted manner. Practice has proved that the quality of the obtained wheat flour is completely different by selectively grinding and extracting flour and non-selectively pulverizing and extracting flour. As far as wheat flour mill plant and equipment operation are concerned, good craftsmanship and equipment are the prerequisite, and correct operation skills are the guarantee. Only in production practice, in strict accordance with the requirements of process design, comprehensive consideration, careful operation, more observation, more analysis, and more thinking. Only in this way can the best process effect be achieved, and the various economic and technical indicators can be guaranteed and improved, and the best powdering effect of high quality, high yield and high efficiency can be achieved.
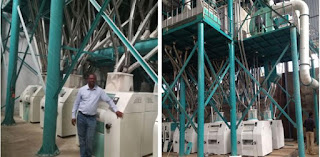
Hongdefa wheat flour mill plant
Our Hongdefa roller mill is European Standards ,with automatic running.
And our factory supply wheat flour mill plant from 20t/24h to 500t/24h with high quality, if you have an interest, you can contact us freely.
Whatsapp/Telephone: +86 150 2815 6279
Email: miya@hdfmill.com
Website: www.hdfmill.com